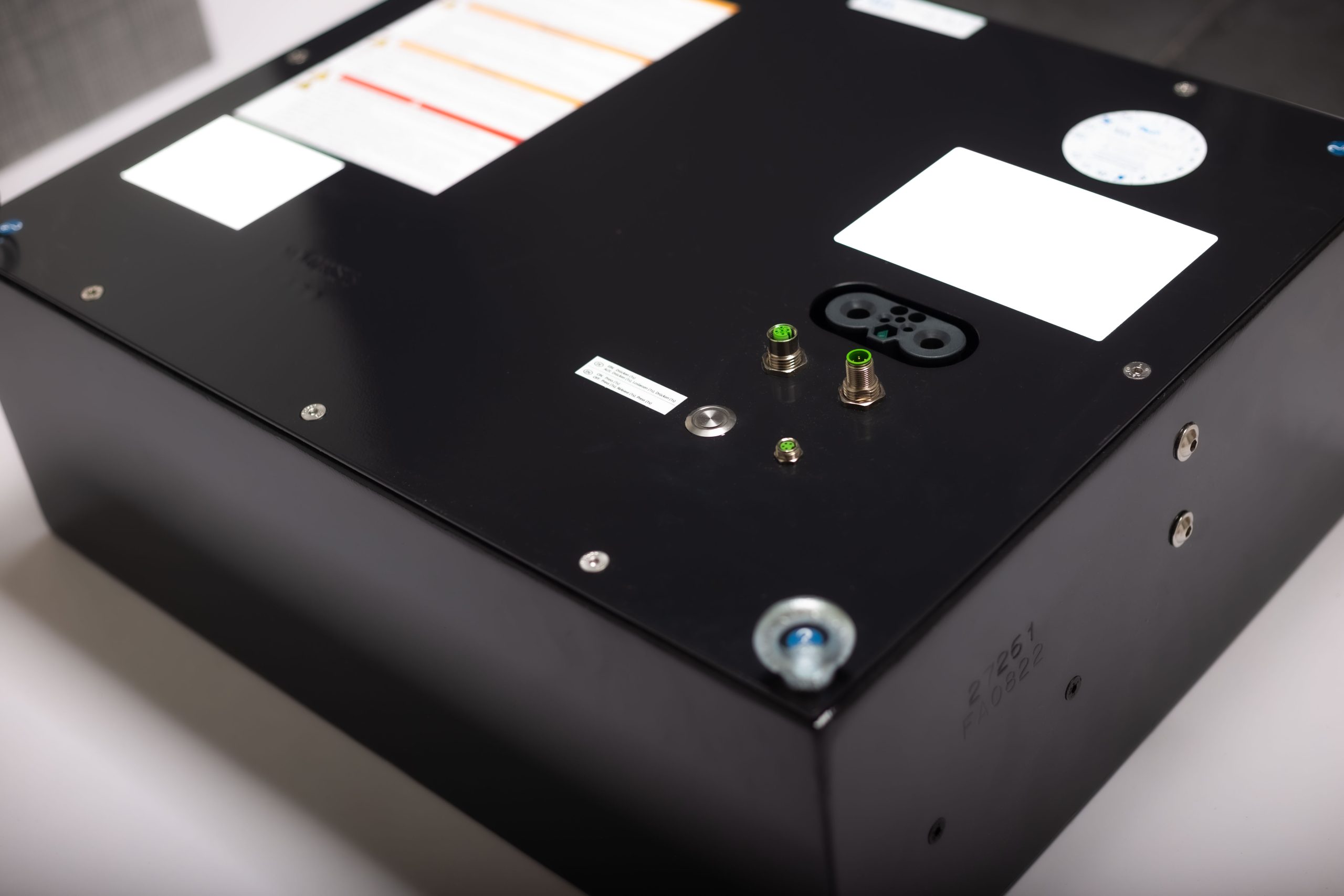
Audi Brussels has been using automated guided vehicles (AGVs) for the production of the Q8 e-tron electric car for many years. The system is part of the assembly line and transports semi-finished products and the Q8’s high-voltage battery to the assembly line. It has been running reliably and stably for over five years. However, over time, components need to be replaced, including proactively – this includes the batteries in the AGVs in particular.
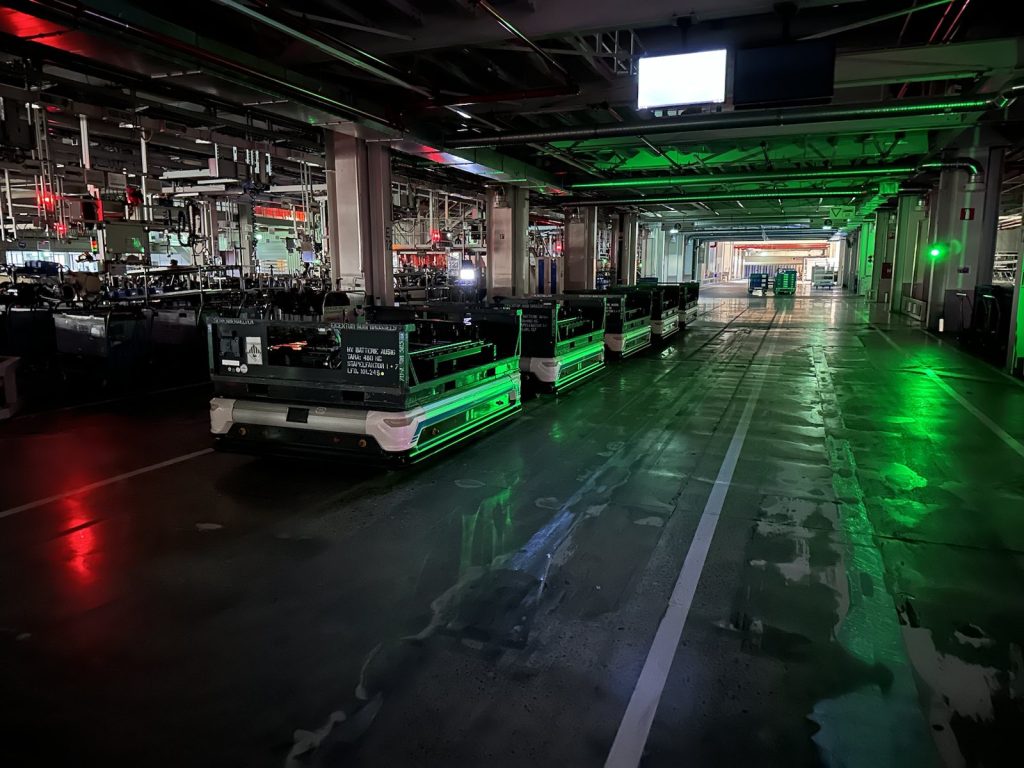
The challenge: replacing outdated batteries
As a long-standing partner of Audi Brussels, we are responsible for the software development, hardware replacement and support of the AGV system. As is usual with lithium-ion batteries, including those installed in AGVs, the performance of the battery drops measurably after a certain, sometimes known, number of charging cycles. This manifests itself in the fact that the AGVs have to travel more and more frequently for charging, as the capacity of the battery continuously decreases. In order to avoid failures and also to maintain the required system throughput, which is impaired by increasingly frequent charging, successive replacement of the batteries was and is necessary. This proved to be a challenge for us, as the batteries in the AGVs were no longer available.
Technical requirements and customized solutions
In order to meet the technical requirements and ensure CE certification, we developed a new battery in collaboration with the industrial battery specialist Allgäu Batterie GmbH & Co. KG, we developed a new battery that was perfectly matched to the old battery. We had to ensure that the dimensions, mounting device (holes), charging behavior and voltage matched exactly.
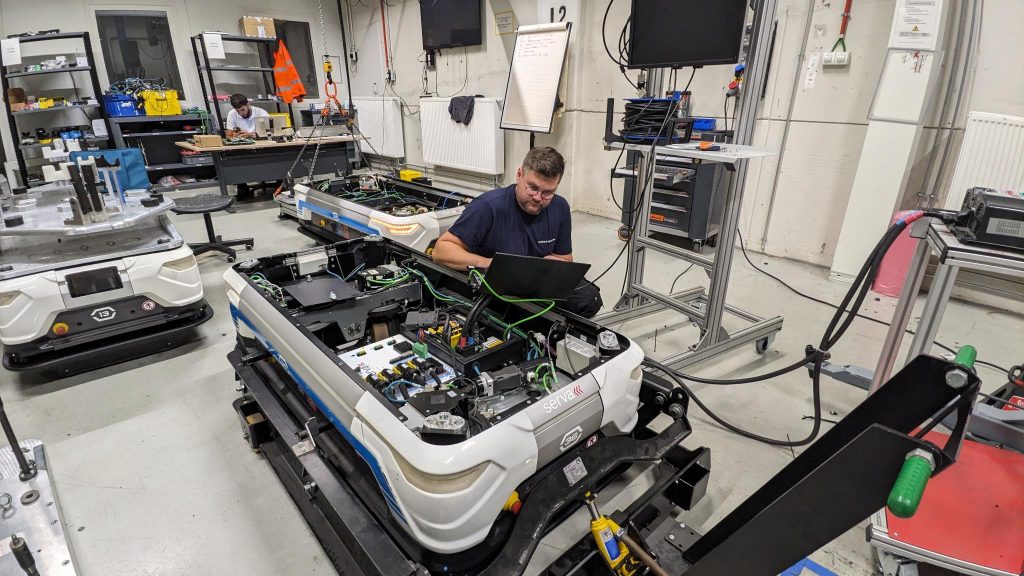
The biggest challenge
The state of the art for many industrial batteries is that their battery management system (BMS), which has various tasks to maximize the battery’s service life, can be addressed via CAN bus communication. However, the BMS of the old battery was connected to the AGV controller via TCP and a proprietary protocol. The data exchanged here included the charge status, current flow, temperature, warnings and other information that the AGV needed to make charging decisions, for example.
The solution: The data required for the operation of the AGV is also provided by the BMS of the new battery, but the AGV has no way of reading out the data via CAN. A Can-To-TCP adapter developed by us creates the necessary compatibility here. This accesses the data from the battery bus via a CAN adapter and translates it into the proprietary format of the AGV software using middleware.
Development and implementation
Using reverse engineering, we analyzed the protocol of the old battery and integrated the BMS from Allgäu Batterie into the AGV via a software adapter. We developed the entire software in the office and did not have a test environment in the form of an AGV.
The success was all the greater when we no longer had to make any adjustments when installing the first battery. The new battery and the AGV software communicated smoothly right from the start.
Conclusion
We are proud that, as specialists in software development, we were able to develop a new battery with the right partners in this situation. With the battery, we meet all technical and regulatory requirements and ensure that the production of the Q8 e-tron continues to be supplied efficiently and trouble-free by the AGVs.
Many thanks to Audi Brussels and Allgäu Batterie for the great cooperation!