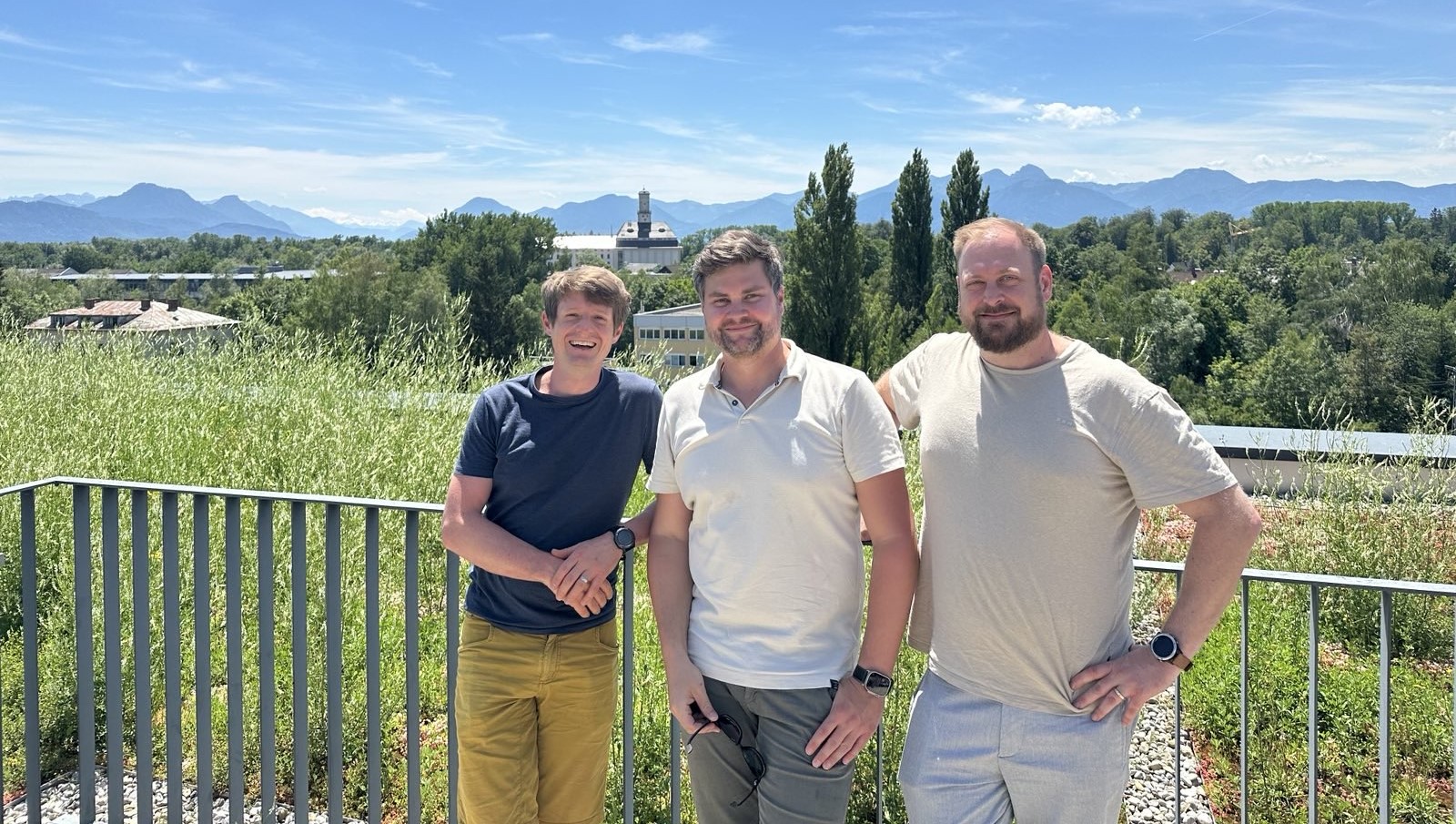
We are Thomas, Thomas, and Marc, three friends who met while studying and share a passion of developing software and enabling others to develop good software.
Following our studies, the three of us pursued diverse careers in software development, working in various industries and for multinational corporations. From backend banking systems to software for autonomous systems and automated guided vehicles (AGV) in intralogistics. This allowed everyone of us to develop our own skills and gain valuable experience—not only in how to do things, but also in how not to do them. Two years ago, we founded Continua Systems GmbH motivated by our specific expertise and a desire to build something new.
Since the company’s beginning, we have focused on intralogistics automation, particularly with AGVs. We assist various firms around Europe with the maintenance, service, optimization, and design of AGV systems.
We recently quit working from home and relocated to the Stellwerk18 incubator, where we are now focused on creating our innovative product, AutomationInsights.
What is AutomationInsights?
Our previous work has made one thing quite evident.
We and the consumer keep asking the same questions. How’s my system doing? Where does it fail? How do I get the most out of my system?
What is the difficulty in addressing all of these questions? It’s time-consuming, costly, and unsatisfactory: hours of Excel pushing, peering at log files, and hurriedly “programming” SQL queries or little tools that you later “throw away” because they’re too particular. This is not what we envision as sustainable software development.
What can you do to be happy again? In most cases, the analytical process can be divided into key components. This marked the beginning of our product AutomationInsights. A product with three modules: log, metrics, and time capsule.
Every analysis is based on data. A lot of data. Specifically, data that is not collected by the deployed server programs for managing AGVs. We acquire this data in a creative and storage-optimized way.
And then what? What do you need to ensure that the system is working smoothly? Evaluations! And by that, we don’t just mean the overall number of completed actions, but much more detailed and meaningful metrics that compare the desired state to the actual state and from there find trends reflect a pattern, because change typically occurs gradually and without being immediately seen. For example, consider the capacity and condition of the batteries in AGVs. Lithium batteries lose capacity over time (extremely slowly). AGVs take longer to charge and require more frequent charging. This influences processes. Eventually, a ‘tipping point’ occurs when previously unknown side effects surface. The highly optimized system is suddenly no longer optimized due to parameter changes. However, this does not imply that everything should be scrapped and redone.
And how is optimization performed?
Typically, maintenance staff or system operators are consulted. The remark frequently looks like this: ‘Yes, I remember a period when I thought… Let me look at it.
This is where our third module comes into play: TimeCapsule. A time machine? Almost. At least for the AGV system. Logs can supply us with such precise data that we can visually portray whole system states, including all logs at the right moments, revealing insights into the system’s decisions.
Are you a systems operator or a process planner? If you know, then you know. TimeCapsule can also be utilized for a variety of different applications.